
extracta PV
Revolutionizing Solvent Extraction
THE EXTRACTION PROCESS
TODAY
Normally, the choice of extraction method depends on various factors, including the type of compounds to be extracted, the raw material, the desired end product, and industry application. Each plant is therefore designed and tailor made for optimizing the peculiar process.
Also, a complete extraction process usually requires many subsequent passages - such as idro-alcoholic or solvent extraction or infusion, product gross separation, filter pressing and finally steam distillation of the residues, etc. Additionally, proper post-processing and purification steps are often employed to further refine and concentrate the extracted compounds for achieving a stable final extract. Finally, source material handling is a actually burden.

Extracta PV Technology incorporates in a single machine all the required steps into a dynamic extraction process, drastically shortening the overall process time by eliminating intermediate handling of the source material and by reshaping the entire production system in a modular way. The fully programmable operational steps of the machine thus allow a freely adjustable process adaptation: from herbs extracts to seed oil extracts up to elasto-polymers removal from textile residues.
DISRUPTING
INNOVATION
EXTRACTA PV TECHNOLOGY
Extracta PV is a unique solution, as it includes an in-built hydraulic press. This allows a more uniform density of loading throughout the extraction process, thus permitting an evenly distributed flow of solvent trough the material.
Once the extraction process is terminated, the same press can also allow a final pressing (10 Kg/cm2) of the material to an almost dry state. Optionally, steam distillation can be used to both dry the material and recover any residual solvent. This can assure a full compostable residue as well as a more environmental friendly approach to herbal extraction processes.
Extracta PV is equipped with a positive displacement pump capable of inducing a programmable forced circulation through the material. This Dynamic Extraction can guarantee exceptional time saving compare with statical extractors (from days to hours).
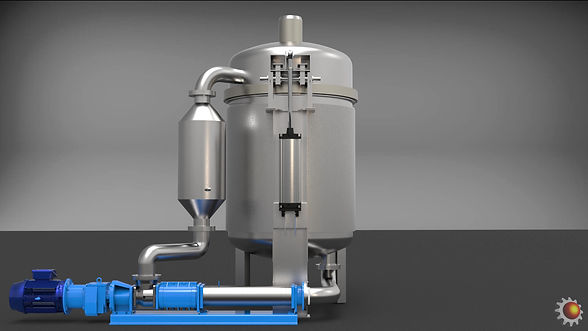


HOW EXTRACTA PV
IS LOADED
Extracta PV is loaded with textile bags filled with all the herbs needed for the extraction process. This solution grants also a cleaner, safer and easy to handle environment for the operators.
Moreover, this solution:
-
Automates the task of lots production;
-
Unifies lot sizes increasing extraction reliability;
-
Improves warehousing by creating palletized, stackable storage, for row and processed material;
-
Drastically reduces handling;
-
Reduce safety risks coming from herbal residues;
-
Improves traceability of lots.


AUXILIARY MACHINES
Extracta PV can be further implemented by two fully automated technologies: the bag filler and the bag unloader, both ATEX certified.


ExtractaPV can be produced in different sizes:
-
A line of lab and semi-production machines with a material volume content ranging from 70 to 120 lt;
-
A line of full production units capable of loading 1 to 3 textile containers with a total volumetric capacity (material) of:
– Single bag: 900 lt;
– Twin bag: 1800 lt;
– Triple bag: 2700 lt.
HOW IT WORKS
An innovative
combined technology
EXTRACTION
By using vacuum technology within the autoclaves, oxygen removal and complete inertization of the working environment are quicker and thorough.
The initial wetting of the process material is instantaneous. The fully programmable and even variable extraction steps allow complex, bespoke extraction cycles.
COMPRESSION
The hydraulic press inside Extracta PV autoclaves can allow a final pressing (10 Kg/cm2) of the material which forces out most of the retained liquid to an almost dry state.
Optionally, steam distillation can be used for drying the material as well as recovering any residual solvent or recover some wanted aromatic notes.
SYNCHRO–EXTRACTION
Extracta PV harnesses the power of Synchro patented concept to obtain the maximum extraction efficiency. The main result of the combination of a Dynamic Extraction and Synchro Extraction is a significant reduction of the extraction time and a better concentration of the final extract with a significant reduction in volume to store or ship.
DISTILLATION
Extracta PV Technology can also allow the packaging of the row material thus simplifying both the handling and the warehousing process.
A set of specific ancillary machines is in fact provided to fill and empty the specially designed textile containers thus improving the overall process automation.
FULL PLANT AUTOMATION
Simplyfing complexity
with a single interface
THE ENTIRE PROCESS
AT A GLANCE
Extracta PV full automation technlogy comes with a 17” color touch screen as HMI interface delivering:
-
Full P&I visual check;
-
Cycle graph of all parameters & variables;
-
Complete history log of all processes.
EXTRACTA PV BENEFITS

TIME SAVING
Vacuum technology allows
istantaneous wetting of the materiali proving a N2 and time saving solution

BESPOKE CYCLES
The low and adjustable liquor ratio needed allows elasticity and adaptation to the needs of the specific process

PROCESS CONTROL
Extracta PV is fully under control and every step of the process is programmable and even variable while extracting

OPTIMIZATION
The extracted material is pressed and almost dried thanks to a 10kg/cm2 internal press optimizing time & losses

HIGHER CONCENTRATION SOLUTES
The Synchro extraction technology allows to reach higher concentration of solutes thus minimizing the need for solvent

RAW MATERIAL
PACKAGING
Extracta PV can allow packaging of the row material simplifying the handling and warehousing thus reducing the overall handling

FULL AUTOMATION
INTERFACE
The 17'' color touchscreen as HMI interface can deliver full P&I visual check, graphs of all parameters and variables and process history log

FULL ATEX
CERTIFICATION
Extracta PV is fully ATEX certified, therefore not posing a Health & Safety threat to workers,
employees, or property
CASE HISTORY
CAMPARI
NOVI LIGURE

In the realm of solvent extraction, Campari Group and POZZI stand at the forefront of pure innovation, reshaping the landscape of herbs extraction and processing through the power of cutting-edge technology. With an unwavering commitment to quality and efficiency, both partners have embarked on a transformative journey that is going to redefine the industry in the next few years.
Harnessing the capabilities of advanced machinery, and state-of-the-art bespoke engineering, this collaboration has challenged not only the way herbs are extracted, processed, and transformed into high-quality products, but also the way these production cycles are conceived nowadays. POZZI solution in fact, focuses on optimizing every step of the process from extraction to the final distillation of herbal extracts and formulations.
One of the key innovations Campari Group is leveraging on is the use of Synchro-Extraction, a patented technology allowing many different types of extraction as well as process efficiency and product diversification. By incorporating in a single machine all the required steps into a dynamic extraction process, Extracta PV eliminates intermediate handling of the source material thus reshaping the entire production system in a modular way. The use of advanced technology ensures that final products maintain their potency and purity, meeting the highest industry standards.
As a result, Campari Group's dedication to advanced engineering is a testament to the transformative power of innovation in the solvent industry.
The company's commitment to both quality and precision sets them apart as a beacon of progress, ushering in a new era of herbal products that are both potent and even environmentally responsible.